GLASS BLOWING WITH KYLE MEYER
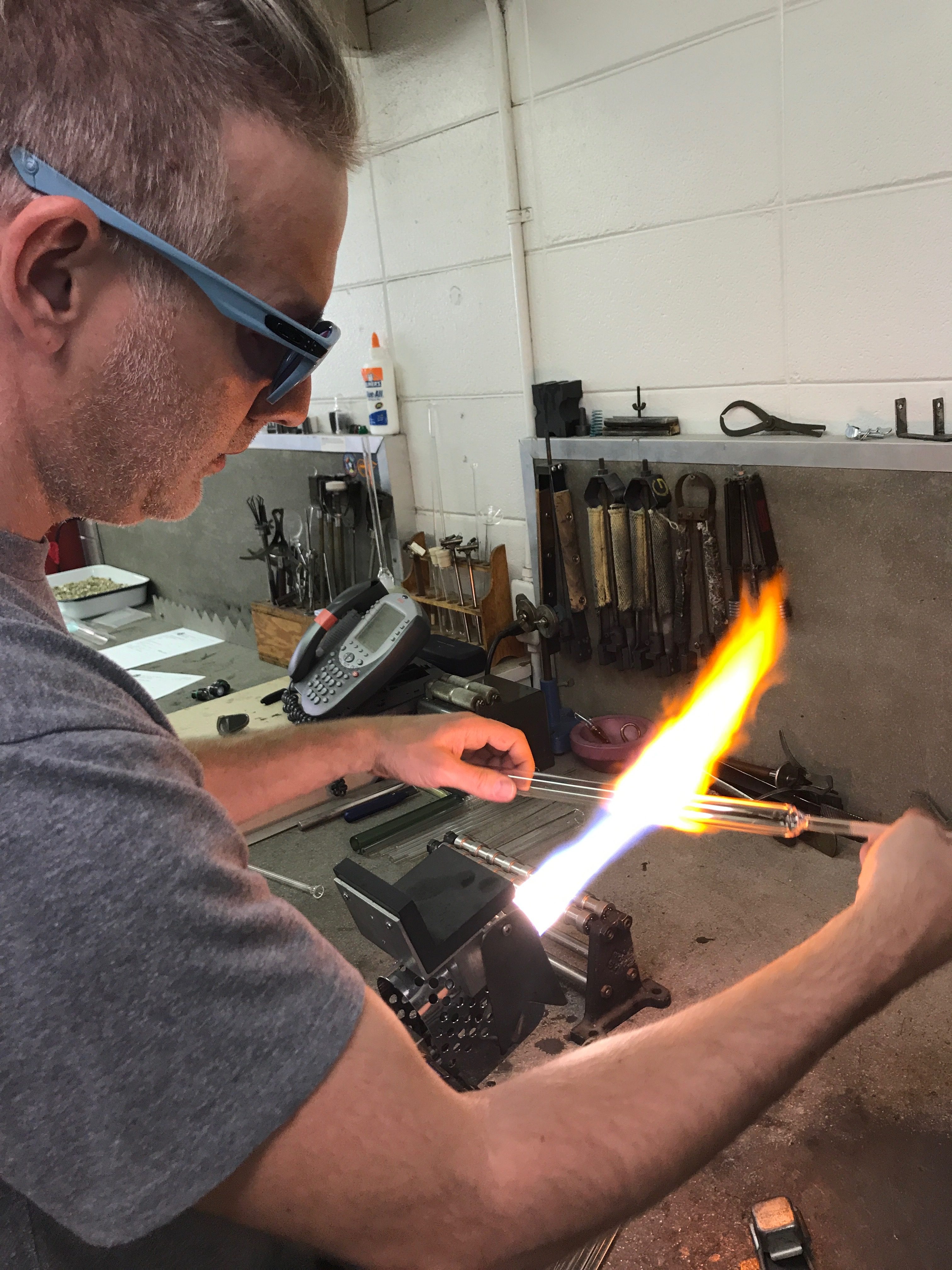
BY SASHA STOGNIY – Kyle Meyer has been the Scientific Glass Blowing Shop Manager at UGA for 3 years. The door to his shop, located in Chemistry 335-337, is always open. Anyone can stop by, and I would highly recommend doing so at least once. Kyle also teaches a Scientific Glass Blowing class (CHEM 7500L). Having taken it the first semester it was offered, I can attest that it was an amazing experience and a very fun introduction to scientific glass blowing. The class is structured with a formal lesson followed by an open lab every week, so students can first master proper techniques and then apply them to create anything they want. I definitely made many memories (and Christmas ornaments) to take home for the holidays. I asked Kyle for an interview because I think his class is truly a hidden gem that everyone needs to know about.
Q: How did you start out in glassblowing?
A: In 2001, I got a scholarship from Sigma Aldrich Chemical – a large chemical company in Milwaukee, Wisconsin – and they sent me to [trade] school in New Jersey for two years. That’s where I learned how to do scientific glass. In return, I agreed to work for them for three years. It was kind of a win-win for everybody. And then I stayed there for 11 [years].
Q: What did you do at Sigma Aldrich?
A: I started off doing a lot of production work. Catalogue items, very basic things: adapters, flasks, traps, manifolds. Then I worked my way up into the customs shop and repairs. When I left, I was doing a lot of custom work and repairs, which I really enjoy.
Q: What is your typical work day like at UGA?
A: A typical day is checking emails, responding to customers, and prioritizing the work that needs to be done in a timely manner. Some people have hard deadlines and others [don’t]. The customer base is anyone at the university. Anybody can come to the glass shop, use the glass shop, and get anything built. And we also do outside work with some pharmaceutical companies.
Q: What kinds of things do you usually make or repair?
A: It can vary from an ampule to a four-position mosquito feeder to fixing stoppers. The work day varies, which makes it very interesting. It’s never the same.
Q: Was there anything that really stood out to you as very interesting or very difficult to make?
A: I’m working on a very intense quartz reactor right now. It has lots of seals, lots of specs, which makes it very hard. It’s very involved. It’s far from basic – it’s very complex.
Q: Will this quartz reactor take a significantly longer time to complete compared to your other projects?
A: Yes. Depending on the job, it can vary from half an hour all the way up to a few hours. This reactor will probably take me a total of 10 hours. There’s a lot going on in it. It’s not all in one piece – there’s other pieces that go into it, probes that connect in, which makes it even more complex than a basic job.
Q: How do you stay connected with other people and news in your field?
A: I’m part of an organization called American Scientific Glassblowing Society (ASGS), which is where I get all of my professional development. There is no more schooling or classes I can take anywhere. This is the only place to learn. You’re learning from a lot of the older guys that have been in the industry or in the universities their entire lives, and they’re passing down information. I go to these conferences and that’s where I learn new techniques, new tools. I also learn about new apparatuses being built. A lot of times you get to see people building glass, which is really helpful because it might not be the way you would build something. And then I also like to go and share my knowledge. A lot of times I’ll go and demonstrate at these conferences or symposiums.
Q: If I remember correctly, one time you brought back a glass slinky, right?
A: Yes, that was a new product someone had developed. They were trying to see how far they could push quartz. They actually pulled it down to .25 mm and wrapped it around a coil, which basically made a glass slinky out of it, which is pretty cool.
Q: What do you usually like to demonstrate at the conferences?
A: I demonstrate what I feel is relevant or exciting for other glass blowers, things they might not see otherwise. Just last week I was in Asheville demonstrating for our section of ASGS and I demonstrated a solvent distillation flask. It was really fun, we had a really great turnout. We had a lot of people involved.
Q: Aside from scientific glassblowing, do you like to make other things?
A: Yep, I like to make art. Around Christmas time, I do a lot of ornaments for people, for friends, for family. I just give them away. I don’t try to sell them or make money. I’d rather give it to somebody so they can appreciate and enjoy it as much as I did making it.
A: Is working with colorful glass for art much different from what you usually do?
Q: The technique is about the same, but when you add that element of color, it makes the glass react a little bit differently. Sometimes it’s a little bit softer, depending on what metals are making the colors, or it could become stiffer. It’s a little bit more exciting, especially when you work with clear all day, to see what kinds of colors you can create, or different patterns, or anything. The possibilities are endless. That’s the beautiful thing about glass, it never stops.
A: What was the vision behind the glass blowing class you teach?
Q: The vision was, when I first got hired on, to get the class going again. It had not been actively running for a few years. It had been one of my goals, taking over this position, to get that class reinstated and active again. I feel like it’s important, not only for the students, but for the university. Glass blowing, over the years, has kind of died out in universities. A lot of positions left, and along with them, teaching opportunities. UGA really has a unique opportunity to offer its students this chance to blow glass and learn techniques that you’re not [going to] get at every other college. A lot of universities might not even have a glass shop. But we have a glass shop that anyone can use, and a class that anyone can take to really learn the basics of what goes in to building an apparatus. It’s a really unique opportunity, and great for the college.
Q: Have you considered a glass blowing club?
A: Yeah, I have. It’s just a matter of… time. Because I’m a one-man shop. It’s just a lot of balancing that would have to go on, getting it set up. But yes, I’d definitely be interested into that in the future. I think it’d be great, and so fun.
Q: For someone who hasn’t taken you class, what tools do you use?
A: For basic tools: a lot of our tools are made from graphite. Graphite has a very good property of withstanding heat, and it won’t leave marks on the glass. We also have to wear glasses to protect our eyes. What other tools do we use? We use some tweezers, a blow hose, and a swivel, and a stopper to be able to blow into the glass to expand it from the inside.
Q: What about tools for heating the glass?
A: We use torches – that’s the major one. Furnace work is usually for soft glass, like what bottles are made out of. The class is flame working, we’re actually using what’s considered a hard glass – borosilicate – a lot of people know it as Pyrex.
Q: What would you say your craziest story with glassblowing is?
A: I’ve been fortunate – I’ve not been seriously injured blowing glass. But it is dangerous – you are working with fire, sharp glass, and sometimes chemicals that can be extremely dangerous. You really have to be well educated on the hazards of blowing glass. I don’t really have any crazy stories, but I have made some very interesting things that have been fun and that have really been able to relate to society in making certain drugs that will help people.
Q: Are your children interested in glassblowing? Do you think they’ll go into the field?
A: You never know. They’re still pretty young – eight and ten. My daughter is more interested than my son. I want to start teaching her to give her the opportunity to see if it’s something she wants to pursue. She seems to want to, but that’s the great thing about raising kids: you just give them a lot of opportunities to see what they really love and excites them and makes them interested. I’d love to have a second-generation glass blower in the family. That’d be really cool. A lot of people in the society are second, third, of fourth generation glass blowers. A lot of these guys and women have years and years of knowledge passed down from their grandfather, dad, and great grandfather. It’s a special part of the society that you’re not going to find in any other organization. There are some textbooks on scientific glassblowing, but a lot of the stuff is passed down from generation to generation.
Q: Can I write about how your wife keeps all the glass from when you just started out?
A: That’s fine, yeah. She has some of my very, very, very, VERY first pieces of glass, that I’m not very proud of. But it just shows where you started. It’s special in that way, to see where I’ve started ad what I’ve accomplished over the years. And she will not get rid of them, [laughs].
Q: Not a question, but Glass Blowing was my favorite class.
A: I’m glad. It is a very fun and interesting class. We learn a lot about glass, we learn a lot of technical techniques, and we also have a lot of fun and create. When students get done with their project, I let them explore. I think there’s something to be said about exploring, that’s part of glass. You have to see what you can do, where you can push it, where you can’t push is. That’s part of learning.
Final author’s notes: in the future, look out for Glass Blowing Club and Glass Blowing II (the continuation to the first semester class)!